Recognizing the Basics and Applications of Plastic Extrusion in Modern Manufacturing
In the world of modern-day manufacturing, the method of plastic extrusion plays a critical duty. Unwinding the principles of this procedure reveals the true versatility and capacity of plastic extrusion.
The Basics of Plastic Extrusion Process
While it may show up complicated, the principles of the plastic extrusion procedure are based on relatively straightforward principles. It is a production procedure wherein plastic is thawed and after that formed into a continual profile with a die. The plastic extrusion procedure is extensively made use of in different industries due to its convenience, cost-effectiveness, and performance.
Different Kinds Of Plastic Extrusion Techniques
Structure upon the standard understanding of the plastic extrusion procedure, it is necessary to explore the various strategies involved in this production technique. Both key strategies are profile extrusion and sheet extrusion. In account extrusion, plastic is thawed and developed right into a continual profile, typically utilized to produce pipelines, rods, rails, and window structures. On the other hand, sheet extrusion creates large, flat sheets of plastic, which are usually further processed into products such as food packaging, shower curtains, and auto components. Each strategy requires specialized equipment and accurate control over temperature and pressure to ensure the plastic maintains its shape throughout cooling. Comprehending these methods is vital to utilizing plastic extrusion successfully in modern manufacturing.
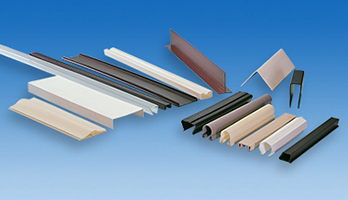
The Duty of Plastic Extrusion in the Automotive Market
An overwhelming majority of components in modern-day cars are products of the plastic extrusion process. This process has revolutionized the automobile sector, changing it into a much more effective, cost-effective, and adaptable manufacturing sector. Plastic extrusion is largely used in the manufacturing of different auto elements such as bumpers, grills, door panels, and control panel trim. imp source The procedure provides an attire, consistent outcome, making it possible for producers to generate high-volume parts with wonderful precision and very little waste. The agility of the extruded plastic components contributes to the general reduction in lorry weight, improving fuel effectiveness. Additionally, the durability and resistance of these parts to heat, cool, and influence boost the durability of automobiles. Hence, plastic extrusion plays a critical role in automobile production.
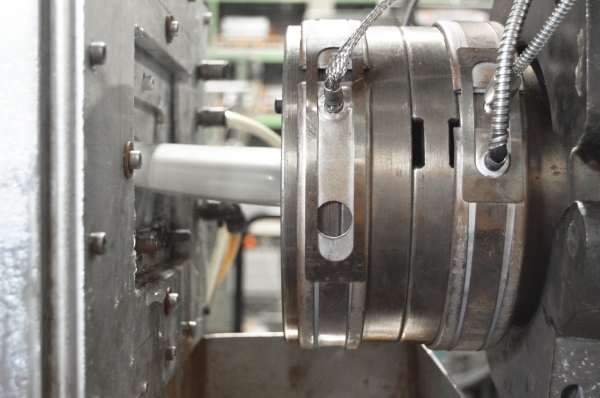
Applications of Plastic Extrusion in Durable Goods Manufacturing
Past its substantial see this effect on the automotive market, plastic extrusion verifies just as Clicking Here reliable in the realm of consumer goods making. This process is important in developing a vast selection of items, from food product packaging to home appliances, playthings, and even clinical tools. The convenience of plastic extrusion enables makers to design and generate complex sizes and shapes with high precision and performance. Additionally, due to the recyclability of lots of plastics, extruded elements can be recycled, decreasing waste and price. The versatility, flexibility, and cost-effectiveness of plastic extrusion make it a preferred choice for lots of durable goods suppliers, contributing dramatically to the market's development and development. The environmental effects of this widespread usage call for cautious consideration, a subject to be gone over even more in the succeeding section.
Environmental Effect and Sustainability in Plastic Extrusion
The pervasive use of plastic extrusion in manufacturing invites examination of its eco-friendly effects. Effective machinery decreases energy use, while waste management systems recycle scrap plastic, reducing raw product needs. In spite of these improvements, even more innovation is required to alleviate the ecological impact of plastic extrusion.
Conclusion
In final thought, plastic extrusion plays an important duty in contemporary production, especially in the automotive and consumer items sectors. Understanding the basics of this procedure is crucial to optimizing its applications and benefits.
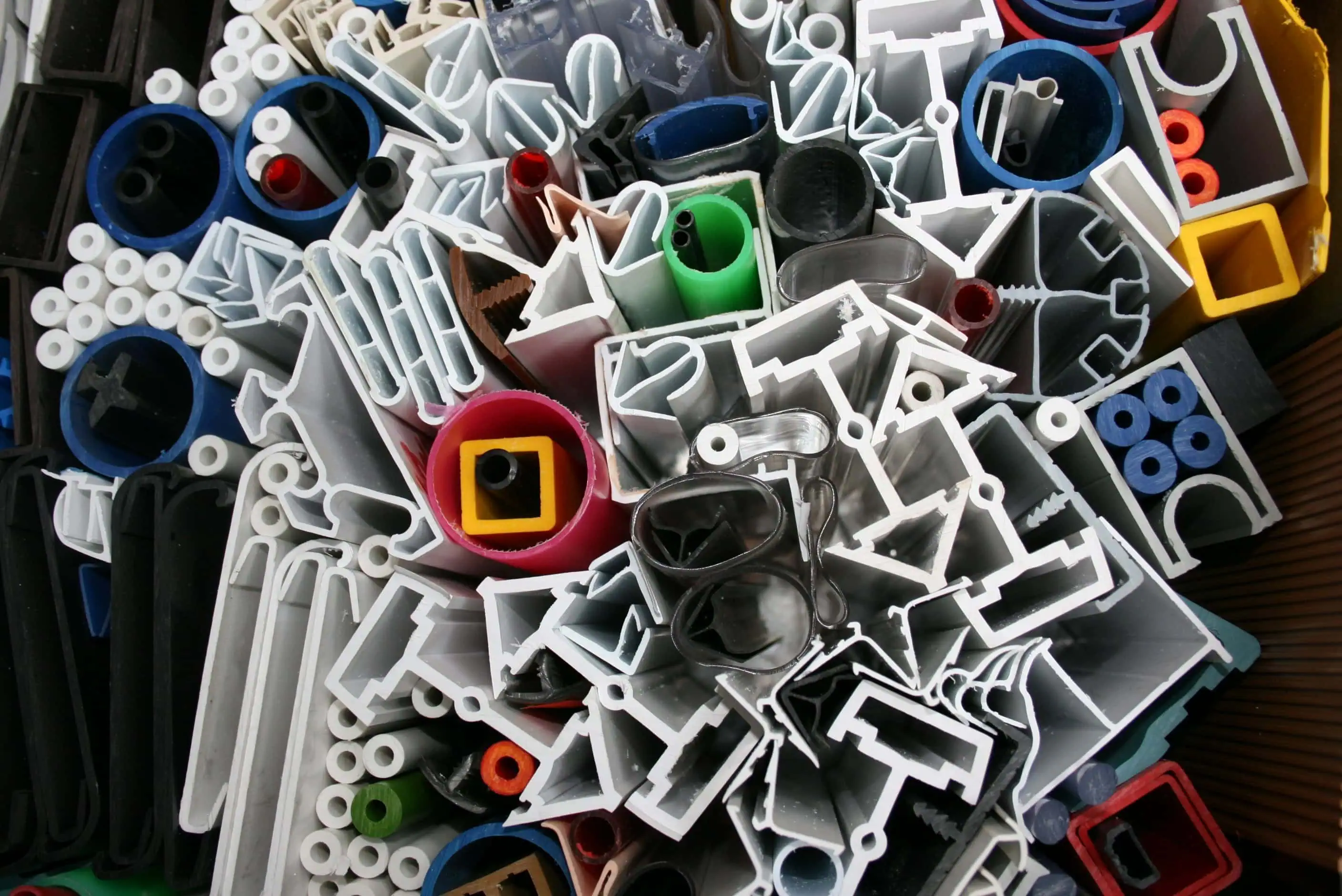
The plastic extrusion process is thoroughly used in various industries due to its efficiency, adaptability, and cost-effectiveness.
Building upon the standard understanding of the plastic extrusion process, it is essential to check out the different strategies involved in this production method. plastic extrusion. In comparison, sheet extrusion creates large, level sheets of plastic, which are commonly more refined into products such as food product packaging, shower drapes, and automobile parts.An overwhelming majority of parts in contemporary vehicles are items of the plastic extrusion procedure